If you think about it, there are so many golf balls in this world. You can find them in stores, golfers’ bags, driving ranges, and golf courses, both in play and lost in water hazards or thick rough. Oh, yes, and plenty are disposed of in all sorts of landfills everywhere. But how are modern golf balls made? What is the technology behind it?
This small, dimpled sphere is the only piece of equipment you use on every hole. You might not be aware of it, but it has come a long way since its humble beginnings in the 16th century. Nowadays it has evolved to be a high-tech marvel of modern sports engineering. The hand-stitched leather balls filled with feathers from centuries ago are distant memories. Now everything is about sophisticated technology and materials to improve performance, durability, and consistency. They keep on evolving with no intention to stop.
In fact, some changes are coming to the golf balls in the next few years. There has been a decision to limit the distance players are reaching lately. The governing bodies, USGA and R&A, have decided on a rollback on how far the balls are allowed to travel. Therefore, shifts coming to golf ball technology and development. Nevertheless, we will explore the new golf balls once they come out. Now let’s have a look into what is going on in the present golf ball manufacturing process.
The Design Phase
The design phase is the critical stage where innovation begins. Here, engineers and designers collaborate closely to craft a ball that pushes performance boundaries and meets legal standards. This phase requires a deep understanding of physics, materials science, and aerodynamics. Also, on numerous occasions, they use a creative approach to problem-solving.
Designers utilize state-of-the-art computer-aided design (CAD) software and computational fluid dynamics (CFD). With this technology, they can visualize and tweak the ball’s features in a virtual environment. It allows them to experiment with different core materials, dimple patterns, and layer compositions. All that without having to produce physical prototypes at every turn. The simulations help in identifying how variations in design elements. For example, how dimple depth and distribution can influence the ball’s flight characteristics. This includes the ball’s trajectory, speed, and stability in the air.
One of the primary goals during the design phase is to achieve an optimal balance between distance and accuracy. Engineers strive to create a ball that maximizes distance for the golfer while maintaining enough spin to ensure control over its landing. The dimple pattern is a key focus in this phase. It minimizes air resistance and enhances lift, allowing the ball to travel farther and with more precision.
Feedback from professional golfers and extensive testing in varied conditions also play a crucial role in the design phase. Manufacturers can tailor the ball’s performance to suit different playing styles, preferences, and skill levels. This makes the design phase a cornerstone of innovation in golf ball technology.
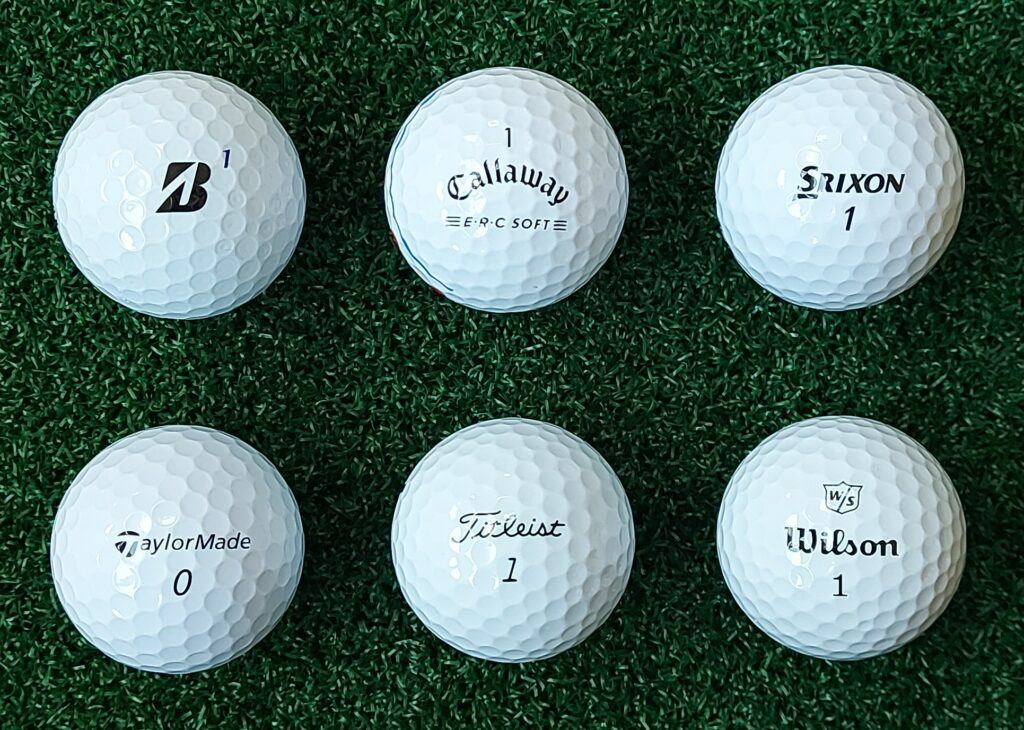
Core Construction
The core construction is where the essential characteristics of distance and feel are primarily determined. A lot of care goes into the design of the core’s composition, density, and hardness. They influence how the ball reacts upon impact with the club. Consequently, they dictate its initial velocity, spin rates, and overall flight behavior.
In crafting the core, manufacturers typically use a blend of synthetic rubbers. Polybutadiene is a popular choice due to its resilient and elastic properties. This material is ideal for achieving the high-energy transfer from club to ball required for long distances. The process begins with the mixing of this rubber compound with various additives that can adjust the core’s final characteristics. These additives might include agents to enhance the core’s resistance to the forces of impact or elements designed to influence the ball’s compression rate.
Once they mix the core material, they then press it and mold it under heat to cure it into a solid, yet responsive, form. The precise conditions of temperature and pressure during this stage are critical. They must be carefully controlled to achieve the desired compression and density of the core.
After molding, they cool and inspect the cores for quality and consistency. Each core must meet strict standards for weight, size, and compression. Variations can significantly affect the ball’s flight and behavior. High-speed cameras and sophisticated measuring instruments are often used during the process. They ensure that each core will deliver the intended performance characteristics.
The Importance of Dimples
The dimples are critical to the ball’s aerodynamic performance. Without dimples, a golf ball would struggle to travel half the distance it currently does. The science behind these small indentations is both fascinating and complex. It hinges on principles of fluid dynamics that govern how air flows around the ball during flight.
Dimples work by creating turbulence in the layer of air next to the ball’s surface. This turbulence reduces the drag force by allowing a smaller low-pressure wake to form behind the ball, thus enabling it to fly farther. The pattern, size, and depth of the dimples have the goal of maximizing distance while ensuring stable flight and accuracy.
Manufacturers experiment with different configurations to find the optimal arrangement that offers the best aerodynamic performance. The total number of dimples can vary from 300 to over 500. Their arrangement, shape, and depth are tailored to influence the ball’s lift and drag characteristics.
Creating the dimple pattern on a golf ball is a precision engineering task. During manufacturing, they use molds to cast the dimples onto the ball’s surface. The quality and consistency of these molds are paramount, as any deviation can affect the ball’s flight path. After molding, each ball is inspected to ensure that the dimples meet the strict specifications for size, depth, and pattern.
The role of dimples in golf ball design showcases the incredible attention to detail. Manufacturers carefully apply the aerodynamic principles to golf balls that help golfers achieve greater distances and better control. This makes the game more enjoyable and competitive.

Layering for Performance
The number and types of layers a golf ball has can drastically affect its performance characteristics. They engineer these layers to manipulate how the ball behaves upon impact, during flight, and upon landing. They tailor it to different styles of play and preferences.
A typical modern golf ball can have anywhere from two to five layers, each with a specific purpose. The layer directly surrounding the core, often called the inner cover, is designed to transfer energy from the strike efficiently. Additionally, it provides the foundation for the ball’s spin characteristics. Materials like ionomer resins are commonly used for their balance of durability and performance. This allows for a responsive feel without sacrificing distance.
The outer layers of a golf ball are where manufacturers really fine-tune the ball’s behavior. They can make these layers from softer materials, such as urethane, which provide a softer feel and increased spin for better control. The outermost layer, or the cover, also plays a crucial role in durability and aerodynamics. It often features a urethane compound that offers a soft feel and excellent resistance to abrasion and cuts.
The process of applying these layers involves sophisticated manufacturing techniques. It has to ensure that each layer adheres perfectly to the next, maintaining the ball’s integrity and performance characteristics. This requires precise control over temperature, pressure, and the chemical composition of the materials used.
High-handicap players might benefit from balls with fewer layers designed for maximum distance and durability. Low-handicap players might prefer multi-layered balls that offer greater control and a softer feel. Layering thus allows for an unprecedented level of customization in golf ball design. It gives players the tools they need to match their equipment to their game.
The Final Touches
This stage encompasses several key processes, including painting, branding, and rigorous quality testing. Each process plays a vital role in the ball’s journey from the factory to the fairway.
The painting process involves applying a durable, protective coating that helps preserve the ball’s integrity against the impacts and abrasions of play. This coating is typically UV-resistant to prevent the color from fading and is designed to adhere firmly to the ball’s surface. The paint also provides a smooth finish that can contribute to aerodynamic performance. It allows the ball to glide through the air with minimal resistance.
Branding is another critical aspect of the final touches. Here they carefully apply the manufacturer’s logo, the ball’s model, and alignment aids. This step requires precision to ensure that the markings are clear, correctly aligned, and evenly spaced. These markings also assist players in identifying their ball and aligning their putts.
Finally, quality testing is perhaps the most crucial part of the final touches. Each ball is subjected to a series of tests designed to verify its size, weight, compression, and overall performance. High-speed cameras and robotic hitting machines measure how the ball reacts to impacts. This ensures consistency in distance, trajectory, and spin. They also test balls for durability. Machines simulate the wear and tear of regular play to ensure that they maintain their performance over time.
Tradition and Innovation
It is hard to believe this much goes into the process of making that little sphere we like to hit so much. But it also goes to show how far the production of golf balls has come. This process starts a long time before you go to the store and buy your favorite golf ball. It also ensures that you can choose the golf ball that fits your playing style.
This comprehensive approach to golf ball manufacturing underscores the sport’s evolution. Every detail, no matter how small, is carefully planned and optimized for performance. It highlights the blend of tradition and innovation that characterizes golf. Now when you understand how your favorite golf ball is made you can appreciate it more every time you hit it.
Which golf ball do you play? Share below!
Related
- Golf Ball Cleaning and Maintenance – Tips for Better Care
- New vs Used Golf Balls – Which Are Better for Your Game?
- What Is the Shelf Life of a Golf Ball?